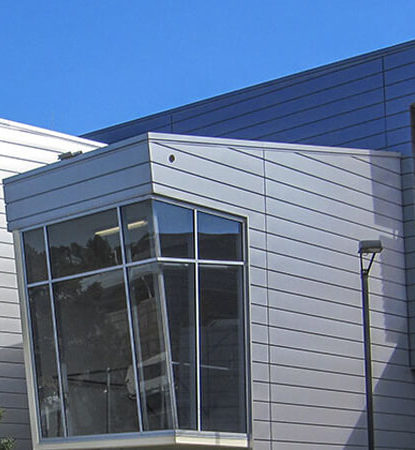
Share this
Use of Metal Panels in Modern Architecture and Design
A vast portion of the architecture around us is heavily accented with metal. We live in an environment where use of metal is increasingly more influential and prevalent. The designers are getting more into the aesthetics of metal. Therefore, in recent years, we could see that the metal is being used in increasingly creative ways in both interior and exterior design.
One of the major reasons for the increasing use of metal is its versatility and the ease to customize. Not many other materials can be perforated, folded, stamped, engraved, and coated in almost unlimited ways.
Another big advantage of metal is its recyclability; many products and types of metals are available with a high recycled content. It’s easy to see the use of a material that not only has indisputable aesthetic advantages, but also its positive environmental footprint.
But, despite the “metal trend” all around us, there are a few things that not every architect and designer is familiar with. Here are a few tips we think are worth knowing before jumping into designing with metal panels:
- CORRUGATION – Everybody likes the look of the flat solid (or perforated) metal sheets. But what actually gives strength to a sheet of metal is the corrugation. That helps immensely with the strength and keeps the metal gauge down, which also means low weight & price. The corrugation of metal prevents the appearance of the “oil canning” effect that no one wants.
- OVER SPECIFICATION – One of an architect’s most common mistakes is specifying an unnecessarily thick metal gauge for their project. Most of the time, a fraction of that gauge is needed and the project falls short when pricing for that heavy gauge comes in. Let the metal manufacturer help you choose the right gauge for your application.
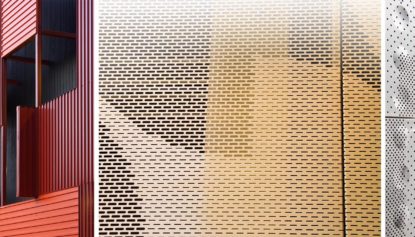
- MANUFACTURER / FACTORY PAINT – Is the best paint you will ever get on those metal panels. It comes with many years of warranty against color fading and scratching. Some installers will suggest powder-coating in order to keep the materials price low. Even the best powder-coated metal panel installed outside will chip in a year or two, and the hassles of removing the panels, repainting, and dealing with the client are not worth the few bucks saved. Educate your client and go with the enameled baked manufacturer factory paint, which most likely is made by one of the biggest names in the paint industry, using the newest and best technology available. Any custom color is available through manufacturer, but for best price, try to stay with standard colors.
- ALUMINUM – There is a misconception that aluminum is much more expensive than steel. For metal panels as a finish product, the aluminum is about 30% more expensive than steel, but is much lighter, costs less to transport, is easier to install, and, above all, it won’t rust.
- THE METAL SHEET GETS FIRST PAINTED, THEN PERFORATED – Therefore at the perforated holes, the bare metal is exposed, and steel will rust if used outside, or in humid environments. Use aluminum.
- THE METAL SHEET IS FIRST PERFORATED, THEN CORRUGATED INTO A PANEL – In order for the metal sheet to be accurately perforated per industry standards, the metal sheets get perforated first, and only then they are corrugated, not the other way around.
- PAINTED METAL PANELS ARE ONLY PAINTED ON ONE SIDE – On the other side is usually found a white or light gray primer. Double sided painted metal panels can always be custom made, but it is usually costly. So keep this in mind when you design a canopy for example, and the panels are visible from both sides. It is sometimes cheaper to specify 2 layers of single sided painted metal, (and you can hide the structural support as well).
- FOR METALLIC LOOK USE MILLFINISH ALUMINUM – No need to use metallic paint and pay extra just to cover that natural great looking metal finish.
- MATCHING COLOR FASTENERS – For painted panels, specify matching color fasteners that should be available at any major metal panel manufacturer.
- PERFORATED PANELS = LESS WEIGHT – It also means lower wind loads and lower strength. Consider all these when designing with perforated panels.
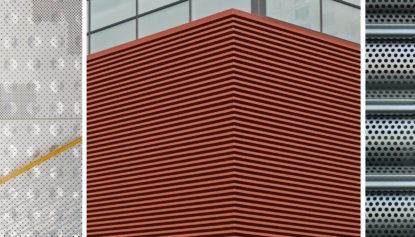
- KNOW WHEN TO USE STEEL – Generally speaking, for the majority of interior applications and for environments where water and other humid factors are not present, the use of regular steel panels, even perforated, is okay. On a large scale project, savings can be achieved when specifying steel instead of aluminum.
- WEATHERING STEEL – Untreated steel panels will naturally rust when exposed to weather elements. They will develop a unique rust drip and can look really unique and beautiful. And is also one of the cheapest materials when it comes to using metal. Ask for a sample and leave it outside at the project site so you can see exactly how it will rust. Each location is different, many natural factors are involved. Sometimes, it will vary on different sides of the same building.
Acids and other controlled oxidant accelerators can be used (mostly for indoor applications), but a clear coat must be used on top of the treatment (which will also bring the price up). - PRICE ON SMALL PROJECTS – On small projects, the price for steel is almost the same as it is for aluminum. It is always a good idea to get both materials priced before proceeding to design, especially on small projects. Always choose aluminum if possible (.040 in) as it is a better product altogether.
- CUSTOM PANELS – there are standard metal panels (that the design and the size of the corrugation cannot be changed) and there are many customizable designs in metal panel industry. Based on the manufacturing process, some panels can be folded and bent in a custom way. Many times you can design your own metal panel section and submit it to the manufacturer. Your design must be in accordance with the manufacturing process & within limits, but working closely with the manufacturer technical support, a unique design can be easily achieved. Most of the time, on a decent sized project, it won’t be any extra charge for creating a custom panel, just make sure to request a sample to see how it looks. Also lead‐time will be longer on custom panels.
- LASER / WATER CUTTING, CUSTOM ENGRAVING – There are many options when it comes to custom cutting and engraving of the metal sheet. Laser and water is mostly used to cut the metal, but sheet thickness and other factors come into play. The process could be quite expensive, also the results can be remarkable. Customer logo or custom patterns can be cut in metal. Free samples will be very hard (if not impossible) to be made. Lead‐time will be long.